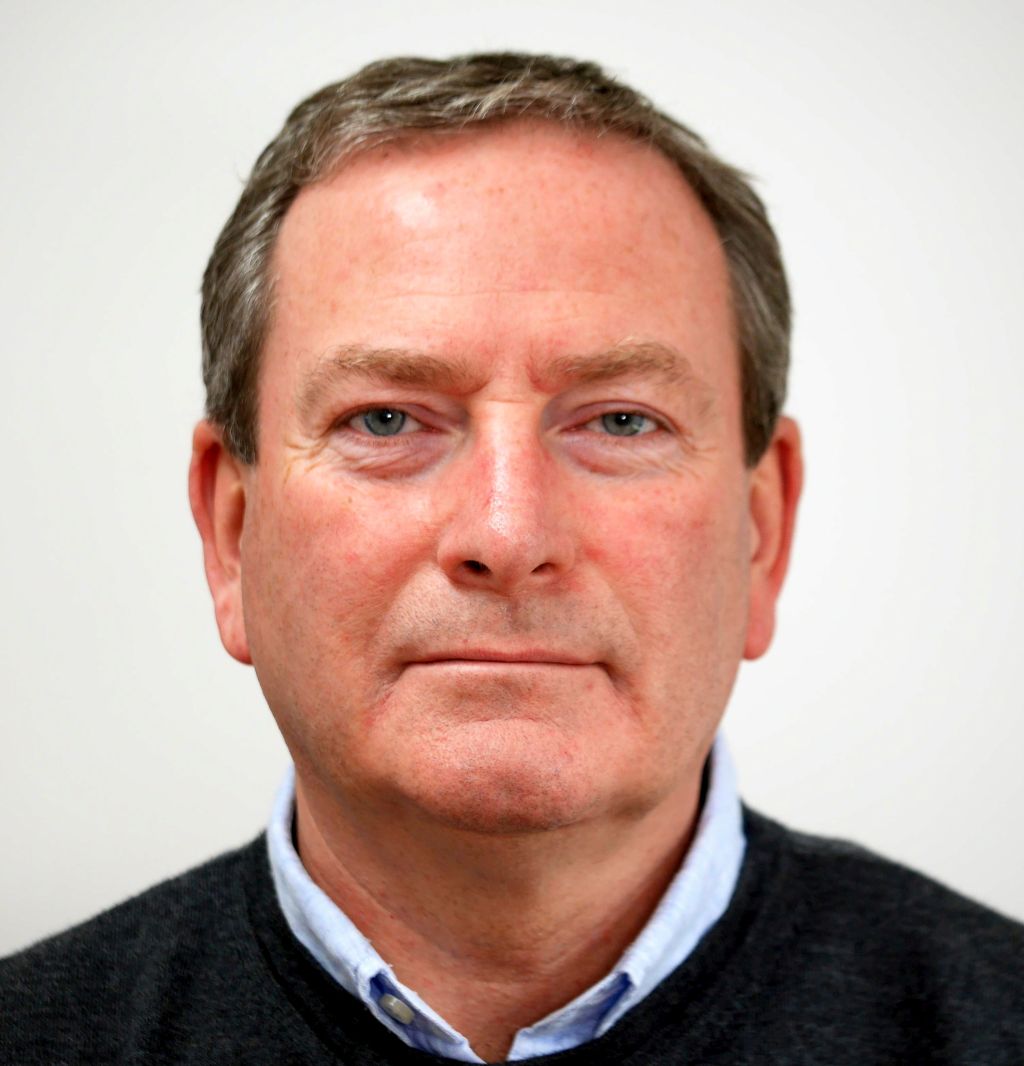
David Boettcher - Professional Engineer
Eur Ing D B Boettcher BSc(Hons) CEng MIET
Providing innovative solutions to engineering and business problems opportunities.
Thomas Newcomen and the Invention of the Steam Engine
Who Invented the Steam Engine?
In July 2012 I visited the Levant mine in Cornwall and saw the beam engine there in steam. This engine was made by Harveys of Hale, one of the two great Cornish makers of steam engines, the other being their great rivals the Copperhouse Foundry, also of Hale. The Levant engine was installed in 1840.
While the guide was describing the engine he mentioned that it had a separate condenser, invented by James Watt, and a lady next to me murmured to her husband, evidently because this was a name she recognised as part of steam engine history. The guide didn't mention the true inventor of the steam engine, Thomas Newcomen, and this incident caused me to reflect on how many people today don't know who invented the steam engine.
For some reason, many people seem to believe the tale that James Watt invented the steam engine after seeing a kettle boiling on a stove and the pressure of the steam lifting the lid. They don't realise that James Watt (1736 - 1819) wasn't even born when Thomas Newcomen (1664 - 1729) together with his assistant John Calley (died 1725) invented the steam engine around 1700 - 1705. In fact, James Watt's father wasn't born when the steam engine was invented; that was in Watt's grandfather's time.
And Newcomen didn't just invent the steam engine; he brought into being a whole new industry to manufacture parts for it. Before Newcomen there was no requirement for large cylinders, thirty or forty or even fifty inches in bore. But the Newcomen engine made it worthwhile to produce and manhandle increasingly massive cylinders, and Newcomen's successors, brilliant engineers such as Smeaton, pushed the boundaries of eighteenth century technology to cast, and machine, and then transport, increasingly large and increasingly more accurate cylinders, so that when James Watt arrived on the scene some sixty years later the difficult work of inventing a whole new sphere of human enterprise had been done, and the way was clear for Watt to improve on what had gone before. Like Einstein after Newton, Watt improved on Newcomen's invention, but in each case the great work, the heavy lifting, the spark of genius, was the work of the first man.
Visiting the Levant mine and seeing the old engine in steam rekindled an interest in Newcomen engines, and the invention of the steam engine by Thomas Newcomen, which is why this page exists. Although there are versions of the true story of the invention of the steam engine on the internet, I wanted to nail my colours to the mast and answer the question "Who invented the steam engine?" as clearly as I could, by stating unequivocally that it was Thomas Newcomen. I also wanted to give a bit more detail about the brilliant breakthrough that Newcomen achieved from an engineer's perspective, which isn't highlighted in any of the accounts that I have read to date.
Forerunners to Newcomen
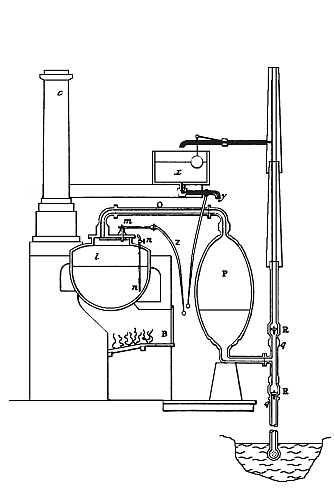
Fig. 1: Savery's pump
Denis Papin
Denis Papin was a French physicist, mathematician and inventor. In 1690 he took a cylinder with a closely fitted piston and lowered the piston down onto a small quantity of water. He then heated the lower end of the cylinder so that the water turned to steam and drove the piston up. When at the top of the cylinder, the piston was held in place by a catch and the steam allowed to condense, forming a partial vacuum under the piston. When the catch was released, the piston was driven down back into the cylinder by atmospheric pressure with sufficient force to raise a 60 pound weight.
Papin didn't take this idea any further. His experiment was a "proof of concept" only, a long way from being a usable steam engine.
Thomas Savery
Thomas Savery invented and patented in 1698 a pump driven by steam which he hoped could be used to drain mines. The Savery pump consisted of one or two receivers and a boiler. A simple cross section of a boiler and one receiver is shown in the figure here, which I have tidied up a bit from the original to make it easier to understand. Each receiver was attached at its base to a vertical pipe between two non-return ("clack") valves "R". The pipe below the receiver which descended into the water to be raised was called the sucking pipe, the pipe that rose up above the receiver was called the force pipe. To operate the pump the handle "Z" was used to open the sector valve "m" and the receiver "P" was filled with steam from the boiler, driving anything in the receiver out and up the force pipe through the upper non-return valve. The steam in the receiver was then condensed by spraying water from the reservoir "x" onto the outside of the receiver via the nozzle "y". The partial vacuum formed in the vessel drew water up the sucking pipe through the lower non-return valve "R", which then closed to prevent its return. Steam was then again admitted to the receiver and the water driven out of the receiver, through the upper non-return valve and up the force pipe, as high as the steam pressure could force it.
Savery's pump had two obvious deficiencies. First, because the steam came into direct contact with the water, and also had to heat the receiver after it had been cooled by the condensing spray of the previous cycle, it was very inefficient thermodynamically - it used a lot of coal. But this was not a fatal flaw and could have been overlooked were it not for its second and major deficiency, it was not very effective at pumping water. The suction side could only raise water up the sucking pipe and into the receiver as high as atmospheric pressure could push it. Atmospheric pressure at sea level is about 14.7 pounds per square inch (psi). The maximum height this pressure can raise water is about 32 feet. To achieve this height an absolute, or Torricellian, vaccum would have to be created in the receiver, which in practice is not possible, and the maximum height a Savery pump could suck up water into the receiver was about 28 feet. There is no theoretical limit to which water could be driven up the force pipe, this being limited purely by the maximum pressure the boiler could raise. In practice, with 17th century materials, this pressure was limited to one or two atmospheres - about 30 to 60 feet above the receiver.
Several examples of Savery's pump were built for raising water for country houses and for fountains, and Savery worked the design up to quite a sophisticated level, with two receivers being used alternately to provide and almost continuous flow of water, and a second boiler to act as a feed heater and pressurised injector to replenish the main boiler when its water level became low. But it was not capable of draining mines, the great commercial challenge and opportunity, and Savery abandoned it in 1705.
Newcomen's Invention of the Steam Engine
Thomas Newcomen (1664 - 1729) together with John Calley (died 1725) invented the steam engine. Although Papin's cylinder was clearly not an engine, some have described Savery's pump as an engine - in fact, it was described as such by Savery himself [Ref. 1] as "an Engine to Raise water by Fire". I am not going to beat about the bush here arguing semantics about the definition of what is an an "engine", all I am going to say is that I know a steam engine when I see one, and Savery's wasn't one. In fact, a very simple and reliable pump called the "Pulsometer steam pump" was designed exactly on Savery's principles of suction by condensing steam and then force by steam pressure - but the clue is in the name: steam pump - it's not an engine. It should be intuitively obvious to even the most casual observer that Newcomen's engine was the first true steam engine, and that it was the invention that kicked off the industrial revolution and the modern world, for good or bad.
James Watt in 1765 made an improvement in the efficiency of steam engines by inventing the separate condenser, which was a very significant invention in terms of thermal engineering, and saved a lot of coal. But it wasn't the same quantum leap as that of Newcomen. Simply stated, before Newcomen's invention, there were no steam engines in the world. After Newcomen's invention, the steam engine existed. Once it existed it could be improved and modified and employed in myriad different applications, but it could only be invented once - and the genius who invented the steam engine was Thomas Newcomen.
Newcomen's Breakthrough
The key to the operation of Papin's cylinder and piston, and to the suction side of Savery's pump, was that when steam was condensed, a partial vacuum was formed and then atmospheric pressure did the work of driving the piston down or sucking water up into the pump. It appears that Papin simply waited for his cylinder to cool naturally. To speed up the cycle rate of his pump, Savery added a spray of cold water to the outside of the working cylinders to cool them more rapidly than they would cool naturally.
We don't know exactly when Newcomen started his experiments or achieved the breakthrough that created th steam engine, but in 1729 Stephen Switzer [Ref. 2] said of Newcomen's engine that "It is generally said to be an improvement of Mr Savery's engine; but I am well informed that Mr Newcomen was as early in his invention, as Mr Savery was in his, only the latter being nearer the Court, had obtained his patent before the other knew it; on which account Mr Newcomen was glad to come in as a partner to it." The first Newcomen engine for which there are definite recorded was erected in 1712 at the Conygree Coalworks near Dudley. However, such an obviously complete and well developed engine installed on a commercial site far away from Newcomen's home would be very unlikely to have been the first, and from Switzer's evidence it would appear that Newcomen had created a working prototype before 1700. There is some evidence that suggests the first Newcomen engine was built in Cornwall at the Wheal Vor mine at Breage. The low thermal efficiency and high cost of coal imported to Cornwall probably doomed this engine.
Mårten Triewald
For ten consecutive years Mr. Newcomen worked at this fire-machine which never would have exhibited the desired effect, unless Almighty God had caused a lucky incident to take place. It happened at the last attempt to make the model work that a more than wished-for effect was suddenly caused by the following strange event. The cold water, which was allowed to flow into a lead-case embracing the cylinder, pierced through an imperfection which had been mended with tin-solder. The heat of the steam caused the tin-solder to melt and thus opened a way for the cold water, which rushed into the cylinder and immediately condensed the steam, creating such a vacuum that the weight, attached to the little beam, which was supposed to represent the weight of the water in the pumps, proved to be so insufficient that the air, which pressed with a tremendous power on the piston, caused its chain to break and the piston to crush the bottom of the cylinder as well as the lid of the small boiler. The hot water which flowed everywhere thus convinced even the very senses of the onlookers that they had discovered an incomparably powerful force which had hitherto been entirely unknown in nature,- at least no-one had ever suspected that it could originate in this way.
Newcomen was born in Dartmouth and he was an iron monger and visited copper and tin mines in Devon and Cornwall as part of his business, so he would have been well aware of the need to pump water from the deep excavations. Savery's pump was clearly unable to meet the requirements for pumping water from deep mines. Whether he knew of the work of Papin or Savery is not known, but somehow Newcomen recognised that a cylinder and piston like Papin's could be used to drive the type of pumps that were already installed in mines, but at the time worked by hand or by animals. There was a report by Dr John Robinson that Newcomen received advice from Dr Robert Hooke, but a search of the papers held by the Royal Society revealed no trace of any correspondence between the two and this story has been discredited.
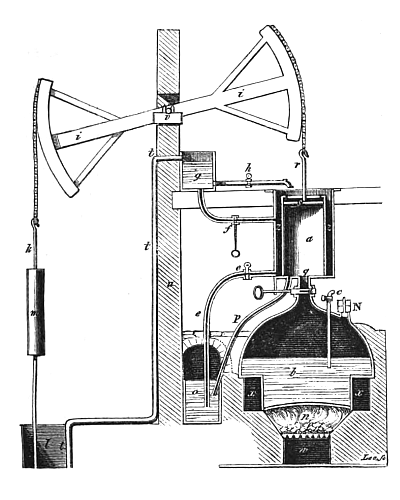
Fig 2: Newcomen's experiment
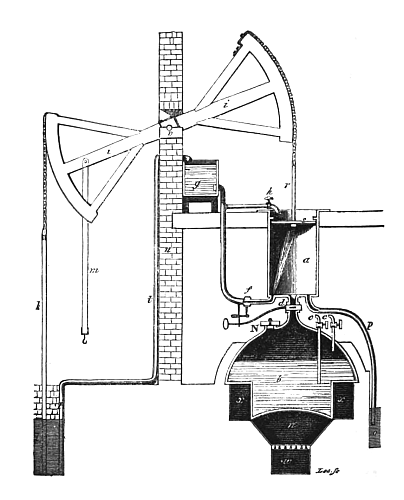
Fig 3: Newcomen's atmospheric engine
With the help of his assistant John Calley, a plumber and glazier, Newcomen assembled a cylinder and piston over a small boiler. To assist the process of cooling the cylinder, Newcomen and Calley arranged a lead jacket around the cylinder. When the piston was at the top of the cylinder, cold water was introduced into this jacket to cool the cylinder and condense the steam within.
But one day, after some ten years of trials, a dramatic breakthrough occurred as related by Mårten Triewald [Ref. 3] in the boxout on the right. The breakthrough was that some of the cooling water introduced into the jacket around the cylinder leaked into the cylinder through a hole in the casting. This cold water immediately started to condense the steam, and as the steam condensed it created a partial vacuum in the cylinder drawing more water through the hole, creating a spray in the cylinder and condensing the rest of the steam very rapidly, creating more of a vacuum in the cylinder with the dramatic results reported by Triewald. (Strictly speaking, the water was forced into the cylinder by the external atmospheric pressure, but many people find it easier to think of the vacuum drawing the water into the cylinder.)
A hole in the cylinder wall, most likely caused by a defect in the casting, had been stopped up with tin solder. Triewald says that the heat of the steam melted the solder, but the low pressure steam Newcomen was using wouldn't have been hot enough to do this. It is more likely that the solder had not fused with the metal of the cylinder and simply was sitting in the defect as a loose plug. Repeated cycles of heating and cooling could have worked it loose, with increasing amounts of water passing it, until the day when it suddenly came out completely. Alternatively, it could be that Newcomen had a cylinder cast with a very thin wall in an attempt to speed up the cooling of the cylinder and formation of the vacuum. It could well be that the first time this cylinder was used a plug of solder that had been used to stop up a hole in the casting let go, or did not block the hole completely and allowed a spray of water into the cylinder. However it came about, this is an entirely convincing explanation of Newcomen's great breakthrough.
It would have been clear to Newcomen that the major problem with a "Papin type" design was the time taken to cool the cylinder and create the vacuum under the piston. No doubt his experiments were designed to investigate ways of speeding this up, and one of the ways that would have been obvious was to use a cylinder with thinner walls. When casting anything thinner and thinner it becomes progressively more difficult to get the molten metal to flow into the narrow parts of the mould, and small holes are often left in the casting. It is quite likely that this is the reason for the hole in the cylinder that was stopped up with solder, and that there was less serendipity involved in the Newcomen and Calley's discovery than was portrayed at the time. If they hadn't been pushing the casting technology of the day to its limits in making thin walled cylinders they might never have made their discovery.
Robert Stuart [Ref. 4] shows the drawing reproduced in Figure 2 which shows the arrangement of Newcomen's experimental apparatus quite well. You can see the jacket around the cylinder and the pipes and valves arranged to allow water in and out of this jacket. Stuart says that this drawing is of an actual engine installed in Warwickshire in 1712, but this is not correct. In this, Stuart, writing over 100 years after the event, is following Desaguliers' [Ref. 5] account, which is second hand and contains numerous errors as well as slights on the intelligence of Newcomen and Calley because they were "not philosophers", and should be taken with a generous pinch of salt. Figure 3 shows the arrangement Newcomen and Calley arrived at after their breakthrough discovery of water injection direct into the cylinder. You can see that the lead jacket has gone and that the valve which previously admitted cooling water to the jacket now admits it direct into the cylinder.
Desaguliers did have some interesting comments to make on cylinders, which shows he understood how important to the Newcomen engine's cycle was the rapid heating and cooling of the cylinder, something that James Watt would later understand and eliminate with his invention of the separate condenser.
"Some People make use of cast Iron Cylinders for their Fire-Engines; but I would advise nobody to have them; because tho' there are Workmen that can bore them very smooth, yet none of them can be cast less than an inch thick, and therefore they can neither be heated nor cool'd so soon as others, which will make a Stroke or two in a Minute difference, whereby an eighth or a tenth less Water will be rais'd. A Brass Cylinder of the largest Size has been cast under 1/3 of an Inch in Thickness; and at long run the Advantage of heating and cooling quick will recompense the Difference in the first Expence; especially when we consider the intrinsick Value of the Brass."
Although Desaguliers says that a large brass cylinder "of the largest size" had been cast with a wall thickness under 1/3 of an inch, the casting technology of the time would not have allowed the very large cylinders that quickly became the norm for Newcomen engines. It is most likely that Desaguliers is referring to the largest cylinders used for pumps, which would have been perhaps six or eight inches, or even a foot diameter, which was small compared to the monster cylinders that Newcomen used, which quickly rose to 60 or 70 inches diameter.
The earliest Newcomen engines had brass cylinders, but Coalbrookdale Ironworks developed the means of casting and boring large iron cylinders which quickly replaced the early brass ones. Coalbrookdale kept a monopoly over the supply of large iron cylinders for more than 40 years, so many engines had cylinders from Coalbrookdale. The boilers and other metal parts were usually made locally, the boilers were fabricated on site from copper sheets, being too difficult and delicate to transport.
Valve gear
Because the first boilers used by Newcomen were not capable of producing much steam, he had to arrange the operation of the engine on a "engine follows boiler" principle. This means that after the engine had made a power stroke, the boiler had to be allowed to recover and make enough steam before another power stroke was attempted. Newcomen automated this by an arrangement that started the next stroke only after sufficient steam had accumulated in the boiler. This consisted of a pipe into the boiler with buoy in it. The buoy had a stem or rod projecting up and out of the top of the pipe. When the boiler had recovered sufficiently the rise in pressure forced the buoy up the pipe, and the stem tripped the injection cock by an attached cord.
Snifting valve
Newcomen found that his first engine would stop working after a while, and eventually discovered that this was due to small amounts of air being admitted to the cylinder with the steam. Water usually contains some dissolved air, and boiling the water released this with the steam. This air could not be condensed by the water spray and gradually accumulated until the engine became "wind logged". To prevent this a release valve called a "snifting clack" or snifter valve was added near the bottom of the cylinder. This opened briefly when steam was first admitted and non-condensable gas was driven from the cylinder. Desaguliers [Ref. 6] said "This is call'd the Snifting Clack, because the Air makes a Noise every time it blows thro' it, like a Man snifting with a Cold".
Engine erection
Newcomen engines were more "assembled on site" than supplied complete from a works or factory. The building was an integral part of the engine, supporting the major parts; the cylinder, injection water reservoir and the beam, so the engine couldn't be "built" without the building. The "builder" was one of a small band of entrepreneurs who contracted to build the engine and then sourced the parts and labour, and supervised construction. Stonier Parrot is one of the more memorable names.
Collaboration with Savery
Savery had obtained a patent on his invention that was widely drawn to include all means of "raising water by the impellant force of fire", which probably would have included Newcomen's engine. Rather than attempt to contests Savery's patent, Newcomen joined forces with him and in 1715 a joint stock company was created to handle licensing engines built under the Savery patent, the "Proprietors of the Invention for Raising Water by Fire". The first seven engines, which were built before 1715, were built by Newcomen and/or Calley. After 1715 the company took licence fees from people who wanted to build engines and Newcomen built no more engines himself. Newcomen died in 1729. The Savery patent expired in 1733, after which anyone was free to build a copy of Newcomen's engine (and Savery's).
It is quite astonishing how quickly Newcomen's invention was rolled out across the UK and Europe, by the time the patent expired in 1733 around 110 to 115 engines had been built, and after 1733 the rate of installation of Newcomen engines continued to accelerate. By the time the first Bolton & Watt engine was built around 1775 there were over 600 Newcomen engines installed, and B&W only made a small percentage of the engines installed after that date up to 1800, when there were nearly 1,500 Newcomen engines and only about 500 B&W.
Although Newcomen engines without separate condensers had a much lower thermal efficiency than a Bolton & Watt engine, there were many circumstances where they were still a better solution. Watt charged a fee for his engines that was based on the saving in the cost of coal between one of his more efficient engines and a Newcomen engine. For e.g. a weaving mill that had to buy coal on the open market this was worthwhile, but of course to a colliery coal was virtually "free" and so a Newcomen engine without a licence fee worked out considerably cheaper.
Efficiency of Newcomen engines
John Smeaton (1724—92) was the first to attempt to evaluate the relative performance of Newcomen engines and to improve their efficiency. Before the science of heat and thermodynamics was worked out in the nineteenth century the operation of a heat engine was poorly understood and developments proceeded by trial and error. Smeaton was the first to compare the efficiencies of different engines and identify which characteristics led to better performance.
Smeaton called his measure the "duty" of the engine, which he defined as the number of pounds of water raised by the engine through a height of one foot when one bushel of coal was burned to heat the boiler. This figure could be used to compare the performance of different engines.
Smeaton selected fifteen engines working on Tyneside engines for study and found that their performance varied widely. At the time the size of the piston was regarded as an important dimension so he worked out the load on the piston area, and found that it varied from 5.42 to 10.9 pounds per square inch. Atmospheric pressure is 14.7 pounds per square inch, so that is the best figure that a "perfect" atmospheric engine could achieve. Given the technology of the time, the engine that was lifting 10.9 pounds per square inch of piston area was doing pretty well, more than twice as well as the one that was only lifting 5.42 pounds per square inch. Smeaton also observed that that the most heavily loaded engine did not return the best duty figure and nor was the engine with the largest cylinder the most efficient, or even the most powerful as had been assumed. The largest of the fifteen engines, which had a 75 inch diameter cylinder, returned a duty figure of 4.59 million, while an engine with a 60 inch cylinder recorded a higher duty of 5.88 million.
Smeaton's duty figure can be used to work out the overall thermal efficiency of the plant, how well the boiler, engine and pump turn the energy of the coal into useful work.
Most early writers seem to have taken the calorific value of coal as 13,500 Btu/lb, which equates to 31,401 kJ/kg, which is a bit on the high side. Most sources seem to agree that bituminous coal contains about 20,000 kJ/kg, with a fairly wide variation depending on the exact composition of the coal. Taking this higher figure would make the efficiencies calculated on the low side.
A million pounds of water is 453,592 kg. One foot is 0.3048m. The work done in raising a million pounds of water by one foot is given by the formula mass x gravity x height = 453,592 * 9.81 * 0.3048 = 1,356,280 joules.
A bushel of coal weighs about 84 pounds and, taking the higher calorific value, contains 84 * 31,401 / 2.205 = 1,196,228 kJ of energy.
So the efficiency of an engine with a duty figure of unity (1) is (1,356,280 / 1,195,228 x 10^3 ) x 100 = 0.1134 percent, and the engine with the duty figure 5.88 million was 0.67 percent efficient. These are low efficiencies compared to today's engines, but the cost of running a Newcomen atmospheric engine compared favourably with the cost of using horses to do the same work, and in a colliery where coal was freely available was much cheaper.
By comparing the dimensions of engines with his results, Smeaton concluded that those with larger pistons and shorter strokes were more efficient. The reason for this is that for a given displacement, as the ratio of bore to stroke diverges from unity the surface area increases, i.e. a cylinder with a bore to stroke ratio of one has the smallest possible surface area to volume ratio. Any deviation from this in either direction increases the surface area exposed to the steam, and consequently the mass of metal that has to be heated and cooled on each cycle. By building an engine with a 52 inch diameter cylinder and seven foot stroke, and paying careful attention to all construction details such as making sure that the piston was a close fit in the bore to reduce losses by leakage, he was able to push the duty rate up to 9.45 million, a thermal efficiency of over 1%. This is still very low, and shows why Newcomen engines were most popular with collieries, where the cost of the coal was a minor consideration.
References
There are 6 referencesRef. [1]: Thomas Savery "The Miner's Friend; or, An Engine to Raise Water by Fire" London 1702 jump back to text
Ref. [2]: Stephen Switzer "An Introduction to a General System of Hydrostaticks and Hydraulicks" London 1729, Volume 2, page 342 jump back to text
Ref. [3]: Mårten Triewald "Short Description of the Fire- and Air-Machine at the Dannemora Mines" Stockholm, 1734 jump back to text
Ref. [4]: Robert Stuart "A descriptive history of the steam engine" London 1824 jump back to text
Ref. [5]: John Theophilus Desaguliers "A Course of Experimental Philosophy" London 1744 jump back to text
Ref. [6]: John Theophilus Desaguliers "A Course of Experimental Philosophy", Vol II London 1744, p. 474. jump back to text
Copyright © David Boettcher, 2006 - 2025 all rights reserved. Please feel free to contact me via the Contact me page.
This page updated April 2019. W3CMVS.